MATERIALS
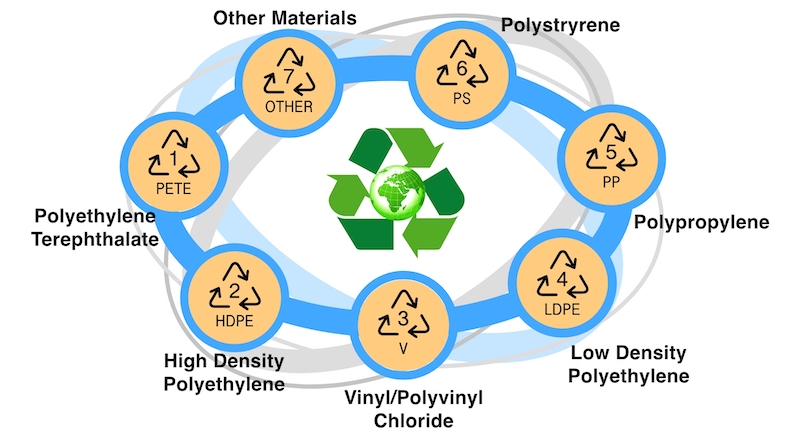
PolyEthylene Terephthalate (PET)
Polyethylene terephthalate (PET) is a thermoplastic polymer resin of the polyester family and is used in beverage, food and liquid containers, food trays, thermoforming and engineering applications. Its excellent wear resistance, low coefficient of friction, high flexural modulus, and superior dimensional stabilty make it a versatile material for designing mechanical and electro-mechanical parts. Because PET has no centerline porosity, the possibilty of fluid absorption and leakage is virtually eliminated giving it excellent barrier properties. PET is globally recognized as a safe, recyclable packaging material. Numerous tests have created a broad scientific consensus that PET is non-toxic and is a safe material for the storage of food and beverages. PET has been proven to be a cost-effective and environmentally friendly packaging option.
High Density PolyEthylene (HDPE)
High density polyethylene (HDPE) is a polyethylene based thermoplastic. HDPE is known for its large strength to density ratio giving it stronger intermolecular forces and tensile strength than LDPE. The difference in strength exceeds the difference in density, giving HDPE a higher specific strength. It is also harder and more opaque and can withstand somewhat higher temperatures upto 100 °C continuously. HDPE is also resistant to many different solvents, has great chemical resistance and high rigidity and has a wide variety of applications in both injection moulding and thermoforming. It is also an excellent choice of material for food related products. Some of the products made with HDPE are bottle caps, food storage containers, pipe fittings, hinges, cutting boards, thermoformed trays, packing trays, etc.
Polyvinyl chloride (PVC) is one of the most widely used plastics in the world. PVC is used in construction because it is more effective than traditional materials such as copper, iron or wood in pipe and profile applications. It can be made softer and more flexible by the addition of plasticizers. PVC has high hardness and mechanical properties. The mechanical properties enhance with the molecular weight increasing, but decrease with the temperature increasing. PVC's relatively low cost, biological and chemical resistance and workability have resulted in it being used for a wide variety of applications. It is used in the manufacture of trays, transparent blisters, pharmaceutical trays, transparent clamshell trays, clothing and upholstery and electrical cable insulation. It is also used in skin packing and a wide range of vacuum formed and thermoformed applications
Low-Density PolyEthylene (LDPE)
Low-density polyethylene (LDPE) is a thermoplastic made from ethylene monomer. It is not reactive at room temperatures, except by strong oxidizing agents, and some solvents. LDPE is widely used for manufacturing various containers, dispensing bottles, wash bottles, tubing, plastic bags for computer components, and various molded laboratory equipment. It is also used in the manufacture of trays and general purpose containers. It is also a good plastic to use for corrosion resistant work surfaces. Since LDPE is a very flexible material it finds a lot of application in the manufacture of parts that require flexibility, Very soft components and pliable parts such as snap-on lids for containers. LDPE is very easily weldable and machinable and can also withstand basic sterilization techniques, including gamma radiation, ethylene oxide gas and disinfectants such as benzalkonium chloride and formaldehyde
PolyPropylene (PP)
Polypropylene (PP) is a one of the most widely used thermoplastic polymers. It is made from the monomer propylene and is rugged and resistant to many chemical solvents, bases and acids. Polypropylene is normally tough and flexible, especially when copolymerized with ethylene. This allows polypropylene to be used as an engineering plastic, competing with materials such as ABS. Polypropylene is reasonably economical and can be made translucent when uncolored. There are three general types of polypropylene - homopolymer, random copolymer and impact copolymer. Polypropylene has good resistance to fatigue and can be extruded, injection moulded, thermoformed and vacuum formed. The large number of end-use applications for polypropylene is often possible because of the ability to tailor grades with specific molecular properties and additives during its manufacture. It is used in a variety of applications including packaging, labeling, textiles, stationery, plastic parts and reusable food containers of various types, disposables, laboratory equipment and automotive components. The melting point of polypropylene is very high compared to many other plastics so it can be used in hot-fill applications and is also microwave and dishwasher safe. Like many plastics, polypropylene has virtually endless uses and it is one of a handful of materials the world is literally built around.
PolyStyrene (PS)
Polystyrene (PS) is a synthetic aromatic polymer made from the monomer styrene, a liquid petrochemical. Polystyrene can be rigid or foamed. General purpose polystyrene (GPPS) is clear, hard and brittle. It is a very inexpensive resin but has a rather poor barrier to oxygen and water vapor and has relatively low melting point. Polystyrene is one of the most widely used plastics and is used in a variety of applications which include protective packaging (such as CD and DVD cases), food containers (such as clamshells), lids, trays, tumblers and disposable cutlery. This plastic can be extruded, moulded, vacuum formed and thermo formed, since it can be cast into molds with fine detail. When blended with polybutadiene it becomes a graft copolymer called High Impact Polystyrene (HIPS). HIPS also has many applications ranging from food containers, packing trays, disposables to industrial moulded products.
PolyCarbonates (PC)
Polycarbonates (PC) are a particular group of thermoplastic polymers. They are easily worked, molded, and thermoformed. Because of these properties, Polycarbonate finds many applications. A balance of useful features including temperature resistance, impact resistance and optical properties positions Polycarbonate between commodity plastics and engineering plastics. Polycarbonate is a durable material. Although it has high impact-resistance, it has low scratch-resistance. The characteristics of polycarbonate are quite like those of Acrylic but Polycarbonate is stronger and usable over a greater temperature range. Polycarbonate is highly transparent to visible light, with better light transmission than many kinds of glass. Unlike most thermoplastics, polycarbonate can undergo large plastic deformations without cracking or breaking. As a result, it can be processed and formed using vacuum forming and thermoforming techniques. It can also undergo secondary fabrication techniques such as bending, drilling, routing, laser cutting etc. Polycarbonate is used to manufacture Electronic Components, automotive and aircraft components, automobile headlights, outdoor fixtures and medical industry applications.
Nylon
Nylon is a generic designation for a family of synthetic polymers known generically as polyamides. Nylon is used for mechanical parts such as machine screws, gears and other low- to medium-stress components previously cast in metal. Engineering-grade nylon is processed by extrusion, casting, and injection molding. Nylon has the ability to be very lustrous, semi lustrous or dull. It has high elongation and excellent abrasion resistance. Nylon can be used as the matrix material in composite materials, with reinforcing fibers like glass or carbon fiber; such a composite has a higher density than pure nylon. Such thermoplastic composites are frequently used in car components where the good heat resistance of such materials makes them feasible competitors to metals
Acrylonitrile Butadiene Styrene (ABS)
Acrylonitrile butadiene styrene (ABS) is a common, versatile thermoplastic used for Engineering and Industrial applications. ABS is derived from acrylonitrile, butadiene, and styrene. ABS combines the strength and rigidity of acrylonitrile and styrene polymers with the toughness of polybutadiene rubber. While the cost of producing ABS is roughly twice the cost of producing polystyrene, it is considered superior for its hardness, gloss, toughness and electrical insulation properties. The most important mechanical properties of ABS are impact resistance and toughness. A variety of modifications can be made to improve impact resistance, toughness, and heat resistance. The impact resistance can be amplified by increasing the proportions of polybutadiene in relation to styrene and acrylonitrile. ABS is processed by the techniques of extrusion, vacuum forming and injection moulding. ABS's light weight and ability to be injection molded and extruded make it useful in manufacturing products such as musical instruments, automotive trim components, automotive bumper bars, medical devices, enclosures for electrical and electronic assemblies, protective headgear, furniture components and panels, luggage and protective carrying cases, small kitchen appliances and toys